Blog
Modular Equipment Design
August 10, 2012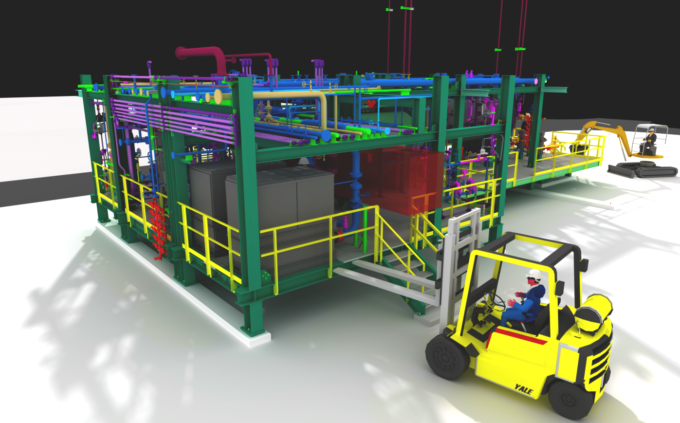
Principal Technology Inc., a provider of total system solutions for natural gas, refining, chemical, process and manufacturing facilities, has the capability to provide modularized process units and equipment designed to minimize the field construction, commissioning, and total installed time to complete a project. The systems range from pre-assembled “black box” sub-systems to fully modularized plug-and-play process units.
“Customers turn to Principal Technology for our design and fabrication capabilities that encompass a broad range of process applications,” said Matthew S. Hodson, P.E., president and CEO of Principal Technology. “By applying our modularization design philosophy, we create packaged equipment systems that contain the technology and capabilities customers are looking for and that can be installed in half the time. This approach means less down-time and minimal impact to existing on-site operations during unit upgrades.”
Principal Technology engineers custom, modularized systems that are manufactured and tested in a fabrication facility then shipped to the customer’s site for installation, final testing and startup. Manufacturing in an off-site shop environment compresses the typical construction schedule because all the labor, equipment, materials, and technical resources are immediately available and there are minimal weather and miscellaneous related delays.
Principal Technology’s modularization philosophy incorporates a purpose driven design approach for the entire project lifecycle. This starts with a traditional 2D and advanced 3D planning study to maximize shop assembled piping, equipment and instrumentation while adhering to the shipping limits of the available transportation modes, according to Hodson. Detailed design includes color coded 3D models and renderings to communicate on-skid, off-skid, and ship loose components to all project stake-holders. “This approach culminates in completed modules with tagged and color coded paint schemes for removable structural shipping braces, temporary anchor bolts and other shipping supports in addition to clearly marked ship loose components allowing for efficient onsite installation, commissioning, and start-up,” said Hodson.
Using this modularized design philosophy Principal Technology has provided a broad range of equipment and systems—from simple pump and filtration skids to gas metering systems to complex modular process units, including sulfur recovery and tail gas treating units and even complete steam generating stations for heavy oil production sites— in one third to one half the time of similar site-built equipment.
Finding the skilled labor required to complete a modern oil and gas production or treating facility can be difficult in some of the remote locations where companies routinely explore for resources. Principal Technology greatly reduces this problem with shop-fabricated modular systems that can be shipped anywhere in the world.
“Principal Technology’s design, system integration, and fabrication capabilities support all stages of a project including evaluation and feasibility analysis, detailed design, procurement, fabrication, commissioning and startup.” said Hodson. “Whether the project scope includes conceptual or detailed design, build-to-print, or design-build responsibilities, Principal Technology has the expertise to implement the project and support the entire project lifecycle.”
Ready to discuss a project?
Reach out to our team to get started
Principal Technology is a full service engineering firm with additional support for system integration, fabrication, sulfur recovery, amine treating, and a wide selection of turnkey solutions.
Call 214-239-3900 or send us a message.